Five weird and wonderful ways nature is being harnessed to build a sustainable fashion industry
One of the greatest challenges faced by the textiles and fashion industry is to make itself more sustainable, not just in terms of economic and labour force issues but in the face of ecological necessity. The production of textiles involves a long chain of complex processes to convert raw materials such as fibres or petroleum into finished fabrics or fashion products.
These processes are typically resource intensive, requiring high concentrations of chemicals, large amounts of water and involving high temperatures and long processing times. This commonly results in high energy consumption and waste.
A transition towards a more sustainable textiles and fashion sector requires approaches that can minimise its environmental and social impacts, therefore opting for cleaner manufacturing processes which can dramatically reduce carbon emissions and water use and eliminate the use of harmful chemicals.
Here are five ways nature is being explored by individuals, research teams and industry to help make fashion more sustainable. Scientists are uncovering and exploiting underlying mechanisms and models found in nature to design new materials, processes and products as well as systems of production for the future.
These range from traditional to contemporary processes that use low or high-tech methods, practised by artists in their studios to scientists in labs or artists and scientists working together collaboratively.
Enzymes as new design tools
Enzymes are highly specific biocatalysts found within the cells of all living organisms. They offer the possibility of manufacturing textiles using simpler and less severe processing conditions which can reduce the consumption of chemicals, energy and water and the generation of waste. As a result, enzymes have successfully replaced a range of industrial textile processes, since they started being used in the early part of the 20th century.
Cellulases and another group of enzymes called laccases are used in the production of stonewashed denim fabrics and garments. Stonewashed effects on indigo dyed cotton denim used to be created by pumice stones – but the use of pumice stones caused damage to both fibres and machines.
Working with colleagues from De Montfort University, I have been investigating the possibilities of using laccase and protease as creative design tools to make industrial textile processes more sustainable.
In our research we used enzymes to synthesise textile dyes and pattern fabrics using ambient processing conditions, such as temperatures as low as 50°C at atmospheric pressure. We now have ways to create many different colours with just a slight alteration of processing conditions, reacting enzymes and compounds together in various different conditions in a technique that eliminates the need to use pre-manufactured dyes.
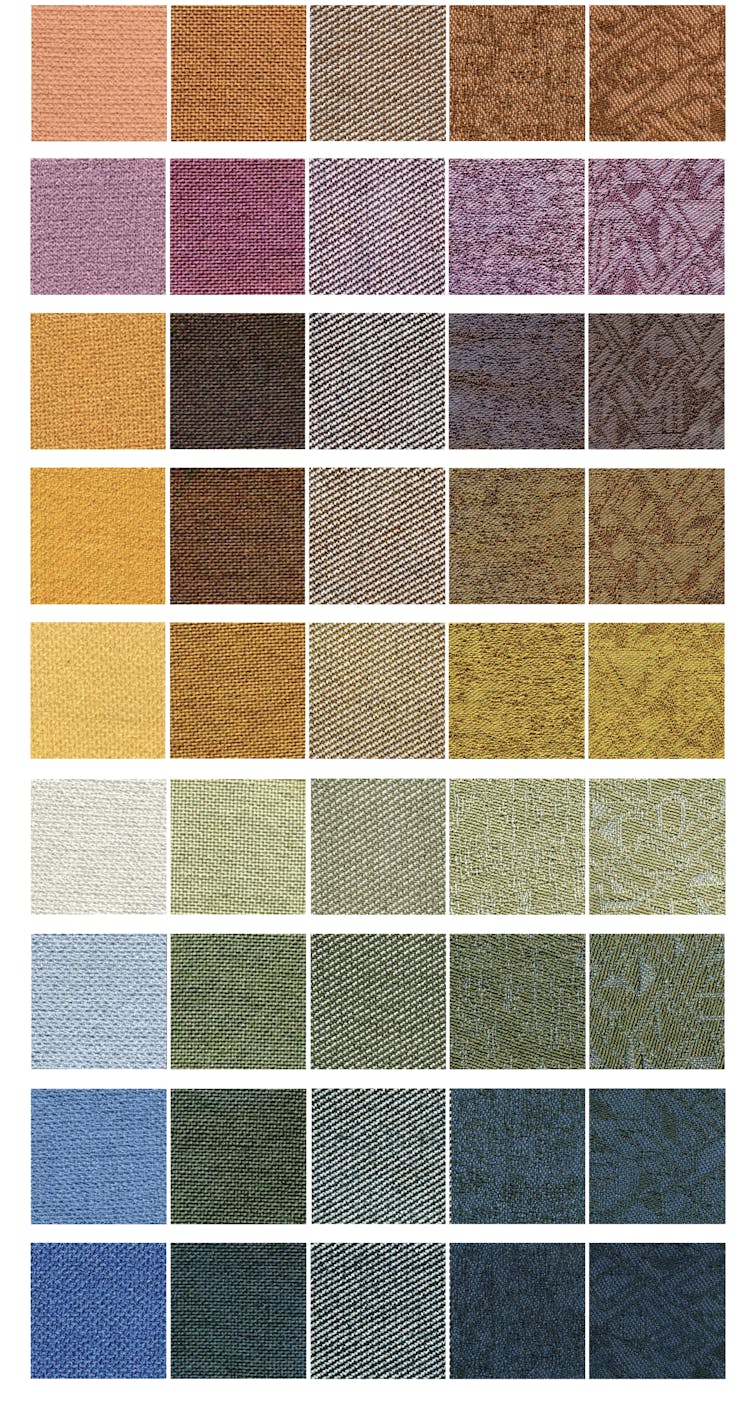
Author
New ways to make leather
From collagen: The area of synthetic biology is growing at a rapid rate, and as a result many companies such as New York-based Modern Meadow are exploring the possibilities this area of modern science offers. The company has successfully bio-fabricated a leather alternative called Zoa.
The advanced material is constructed from collagen (a protein) – the main component of natural leather – but Zoa is designed and grown in a lab from animal-free collagen derived from yeast.
The material is capable of replicating the qualities of leather and offers new design aesthetics and performance properties not previously possible – while also eliminating the high environmental impact of raising cows and tanning their hides (which is often a toxic process).
From fungi: Similarly, San Francisco-based MycoWorks – among others – has been exploring the possibilities of creating sustainable materials using fungi. Mycelium, (a mushroom root material) which is grown from fungi and agricultural byproducts is custom engineered in a lab using a carbon negative process.
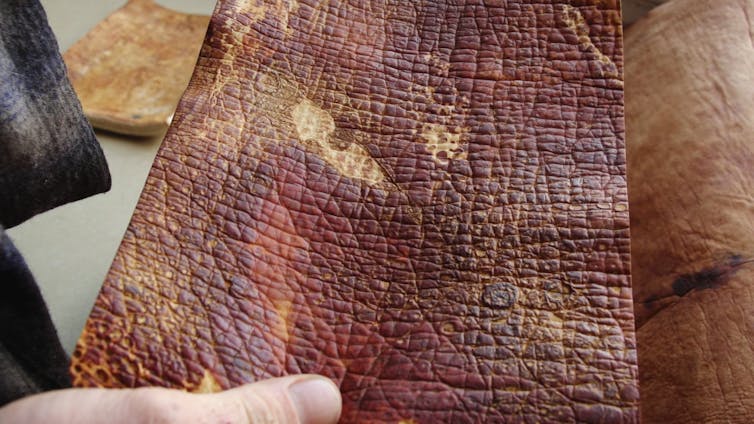
MycoWorks
It is easy to cultivate, fast growing and can be easily manipulated to adopt the properties similar to leather and many other mainstream materials such as wood and polystyrene.
Field work
Grass roots: An interesting project by the artist Diana Scherer called Interwoven explores the fabrication of materials using living plant networks which could be used to construct garments of the future. She has developed a process which manipulates oat and wheat plant roots to grow intricate lace-like textile materials.
She buries templates in the soil that act as moulds, which manipulates and channels the plants root systems to reveal woven structures constructed from geometrics and delicate motifs once the fabric is excavated.
Cow manure: In a circular economy model, nothing is considered waste. In the Netherlands, a company called Inspidere has developed a method it has called Mestic that uses cow manure to produce new textiles. The processing method enables cellulose to be extracted from manure to produce two materials, viscose and cellulose acetate.
The manure is separated and processed in a lab to extract pure cellulose, which is further processed to create viscose (regenerated cellulose) and cellulose acetate (bio-plastic), both of which can be turned into textiles. The group have achieved lab-scale success, the challenge remains to scale this process up commercially.
These are just a few of the ways in which nature is being harnessed to provide the textile and fashion industry with realistic and viable options to move towards sustainability.